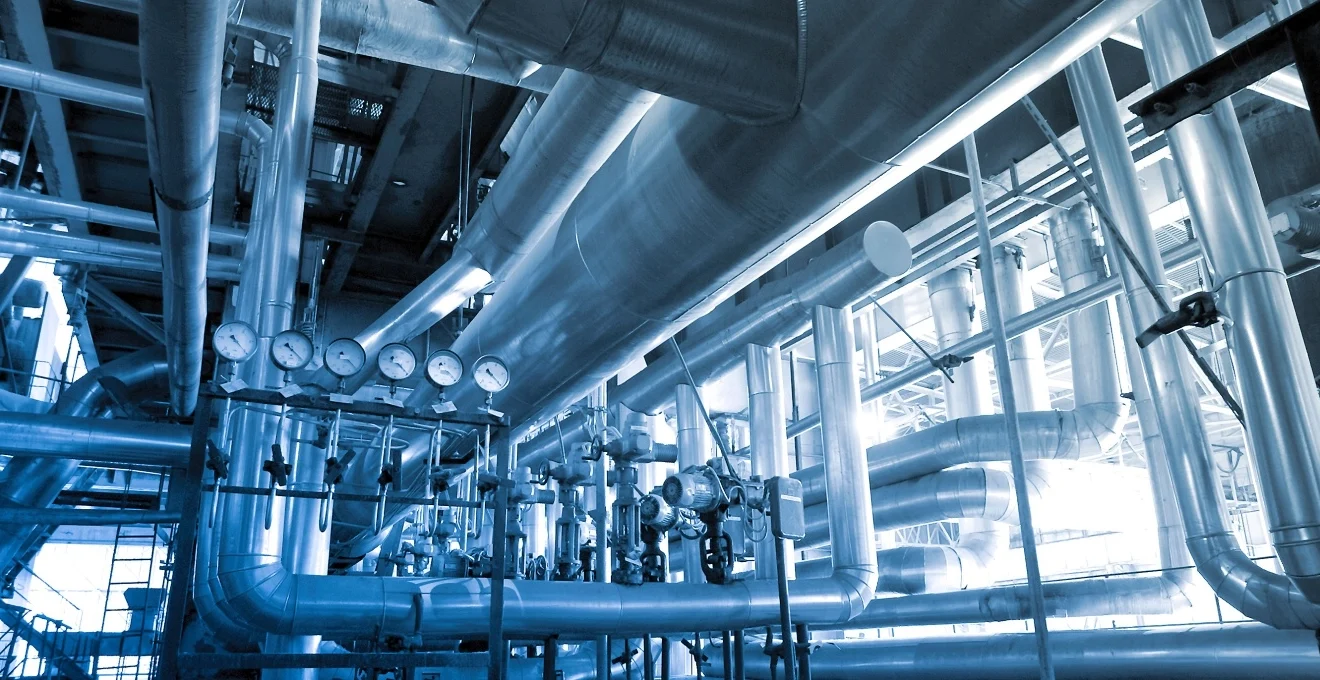
La chaleur excessive dans les environnements industriels met en péril la productivité et la performance des entreprises. Lorsque les températures sont élevées, les sites de production doivent revoir leurs stratégies pour garder des conditions de travail correctes. Les répercussions de la chaleur se font ressentir tant sur le plan humain que technique, affectant alors la rentabilité des opérations industrielles.
Conséquences mesurables de la chaleur sur la performance industrielle
Analyse thermique des zones sensibles en environnement industriel
Les fours et les zones de soudage dans les usines sont particulièrement vulnérables aux changements de température. L’utilisation de systèmes de refroidissement industriels, comme le refroidissement adiabatique, peut aider à garder des températures précautionneuse. Notamment, la brumisation industrielle est recommandée pour ces espaces de stockages.
Données statistiques sur la baisse de productivité selon la température
L’augmentation du stress thermique réduirait l’intensité du travail et nécessiterait des pauses supplémentaires, entraînant des pertes de productivité. De plus, l’Organisation Internationale du Travail (OIT) a estimé que d’ici 2030, l’augmentation du stress thermique pourrait entraîner une perte de productivité équivalant à 80 millions d’emplois à temps plein.
Cette prévision alarmante repose sur une hausse globale des températures qui affectera les capacités physiques et cognitives des travailleurs, en particulier dans les secteurs manuels comme l’agriculture, la construction ou l’industrie lourde. Les régions tropicales et subtropicales seront les plus exposées. En complément des effets sur la santé, le stress thermique est un frein réel au rendement, à la qualité d’exécution et à la continuité des opérations. Sans mesures d’adaptation, les conséquences économiques pourraient dépasser 2 000 milliards de dollars à l’échelle mondiale, selon les estimations de l’OIT.
Effets physiologiques sur les opérateurs en conditions extrêmes
Le travail à la chaleur peut affecter les capacités physiques et mentales des opérateurs. L’Organisation internationale du travail (OIT) indique la productivité commence à diminuer lorsque les températures dépassent 24 à 26 °C, et peut chuter jusqu’à 50 %, si la température dépasse 33 à 34 °C, notamment dans les métiers physiquement exigeants comme l’agriculture ou la construction.
Ce phénomène s’explique notamment par une thermorégulation insuffisante du corps humain, provoquant une déshydratation, une perte de vigilance et un allongement des temps de réaction. Dans les secteurs à forte intensité physique, ces effets peuvent entraîner des erreurs, des accidents ou des interruptions répétées de l’activité.
Conséquences sur la fiabilité des équipements industriels
Les températures élevées ne nuisent pas seulement aux opérateurs : elles compromettent aussi la fiabilité des équipements. Les équipements industriels, notamment les composants électroniques, et en particulier dans les armoires de commande, les variateurs de fréquence ou les capteurs peuvent voir leur durée de vie réduite en cas de fonctionnement à des températures élevées. Bien que les chiffres puissent diverger, il est généralement admis que des températures excessives peuvent affecter la fiabilité et la longévité de ces équipements.
Au-dessus de leur température de fonctionnement adéquate, la durée de vie de ces composants peut être réduite. Ce phénomène augmente les risques de panne, de maintenance imprévue et d’arrêts de production coûteux. Une gestion thermique adaptée est donc indispensable pour préserver le fonctionnement du parc machine.
Technologies de refroidissement nouvelle génération
Systèmes adiabatiques intelligents pour grands espaces
Les systèmes de refroidissement adiabatique sont une évolution majeure en matière de climatisation industrielle éco-responsable. En utilisant le principe naturel de l’évaporation de l’eau, ces systèmes permettent de réduire la température intérieure des bâtiments de 6 à 12 °C en consommant moins d’énergie que les systèmes de climatisation traditionnels. Cette efficacité énergétique est obtenue sans recours à des gaz réfrigérants nocifs, réduisant ainsi l’empreinte carbone des installations. Certaines installations innovantes utilisent aussi des membranes protectrices sur les condenseurs, ce qui évite les dépôts minéraux et renforce la durabilité du système. Ces technologies présentent désormais une alternative sérieuse, conciliant performance thermique et respect des enjeux environnementaux.
Systèmes de climatisation industrielle éco-responsable
Les systèmes de climatisation industrielle modernes adoptent de plus en plus des réfrigérants naturels, tels que le dioxyde de carbone (CO₂) et l’ammoniac (NH₃), en raison de leur faible empreinte environnemental et de leur efficacité énergétique. Le CO₂, par exemple, est reconnu pour sa capacité à fournir une réfrigération durable et écoénergétique dans divers contextes industriels . De même, l’ammoniac est largement utilisé dans la réfrigération industrielle pour son faible coût et son excellent coefficient de transfert thermique .
Par ailleurs, l’intégration de systèmes de récupération de chaleur dans les installations de climatisation industrielle permet de réutiliser l’énergie thermique excédentaire pour d’autres processus internes, améliorant ainsi l’efficacité énergétique globale. Ces nouvelles technologiques, combinées à l’utilisation de réfrigérants naturels, contribuent à réduire l’empreinte carbone des installations industrielles en maintenant des performances de refroidissement adaptées.
Innovation en ventilation stratégique zonée
La ventilation zonée intelligente utilise des algorithmes prédictifs pour adapter en temps réel la circulation de l’air selon les besoins de chaque zone industrielle. Température, humidité, occupation et conditions extérieures sont analysées pour ajuster automatiquement les flux d’air, assurant ainsi un confort thermique constant sans gaspillage énergétique.
Ce type de gestion permet de réduire notablement la consommation. L’usage de contrôleurs prédictifs de modèle (MPC) ou de systèmes moto-régulés, associant capteurs, équipements performants et algorithmes, a montré une forte baisse des dépenses énergétiques dans plusieurs installations. Ces innovations participent activement à une régulation thermique fine et plus sobre.
Automatisation du contrôle thermique par IA
L’intelligence artificielle révolutionne la régulation thermique dans les environnements industriels. En s’appuyant sur des données en temps réel — température, taux d’humidité, occupation des espaces ou encore horaires de production — les systèmes automatisés pilotent les installations de chauffage, ventilation et climatisation (CVC) avec une grande précision. Cette réactivité permet de garder un niveau de confort thermique constant, en réduisant les pertes énergétiques liées aux ajustements manuels ou aux surconsommations.
Les technologies prédictives sont capables d’anticiper les pics de chaleur ou les baisses d’activité, en adaptant le refroidissement de manière progressive. Cette intelligence adaptative permet d’une part d’économiser de l’énergie, et de l’autre, de limiter l’usure prématurée des équipements, renforçant ainsi leur durabilité et la stabilité des installations dans le temps.
Aménagements structurels pour la régulation thermique
Matériaux isolants haute performance pour toiture industrielle
La prévention des risques liés à la chaleur dans les bâtiments industriels repose sur l’utilisation de matériaux isolants performants. Des dispositifs tels que les panneaux composites à haute densité et les revêtements réflectifs de nouvelle génération limitent le transfert de chaleur, ce qui améliore l’efficacité énergétique des infrastructures. Ces innovations contribuent également à stabiliser les températures intérieures, réduisant ainsi la dépendance aux systèmes de chauffage et de climatisation.
Les matériaux modernes procurent des performances thermiques exceptionnelles, avec des coefficients de résistance thermique jusqu’à 40 % plus élevés que ceux des méthodes traditionnelles. L’intégration de systèmes d’isolation multicouches ou de toitures végétalisées industrielles est déterminante dans la prévention des risques thermiques. Ces technologies assurent un meilleur confort pour les occupants en diminuant les coûts énergétiques.
Conception bioclimatique des bâtiments industriels
La conception bioclimatique consiste à exploiter la circulation naturelle de l’air et à orienter les bâtiments de manière optimale pour réguler la température intérieure sans recourir excessivement aux systèmes de climatisation. Cette méthode permet de réduire la température intérieure de 3 à 5°C en été, en adaptant l’exposition au soleil en conséquence et en favorisant la ventilation naturelle.
En intégrant des matériaux à haute inertie thermique et des ouvertures judicieuses, les bâtiments industriels peuvent limiter leur dépendance aux options énergétiques extérieures. La conception bioclimatique participe ainsi à la prévention des risques thermiques en réduisant la consommation d’énergie et l’empreinte carbone des installations industrielles.
Systèmes de récupération et valorisation de la chaleur
Les systèmes de récupération de chaleur permettent de réutiliser l’excédent thermique, par exemple, pour le préchauffage de l’eau ou pour le chauffage des locaux en période froide. En réutilisant cette chaleur excédentaire, il est possible de réduire la consommation énergétique d’un site industriel, permettant ainsi une alternative efficace pour minimiser les coûts énergétiques.
Ces systèmes, basés sur des technologies comme les cycles ORC (Organic Rankine Cycle), permettent de transformer une contrainte en ressource, réduisant la dépendance aux sources d’énergie externes et contribuant à une diminution de l’empreinte carbone. Par exemple, des entreprises utilisant ces alternatives peuvent économiser plusieurs milliers d’euros par an, selon la taille et le secteur de l’industrie.
Gestion des environnements thermiques industriels
Les entreprises industrielles doivent adopter des stratégies organisationnelles et réglementaires adaptées au conditions thermiques extrêmes. La gestion thermique nécessite une méthode globale qui comprend l’adaptation des pratiques de travail, la conformité aux normes et une analyse économique des investissements. Ces mesures contribuent à maximiser la productivité et à assurer la sécurité des travailleurs, en réduisant les coûts opérationnels à long terme.
Gestion des horaires de travail pour minimiser les conséquences thermiques
L’adaptation des horaires de travail est une mesure importante pour réduire les effets de la chaleur sur la productivité. Par exemple, une étude de la Harvard T.H. Chan School of Public Health suggère que le travail en extérieur devrait être limité pendant les périodes les plus chaudes de la journée. Il est recommandé de déplacer les heures de travail à des moments plus frais, par exemple tôt le matin ou en fin de journée. Ces ajustements aident à préserver un rendement plus élevé en minimisant la fatigue thermique et en préservant la concentration des travailleurs.
Les pauses supplémentaires sont également un atout pour assurer la productivité lors de fortes chaleurs. Augmenter la fréquence des pauses permettrait de réduire de manière conséquente la fatigue et les erreurs de travail chez les employés exposés à des températures élevées. L’introduction de périodes de repos régulières dans des espaces climatisés ou ombragés aide les travailleurs à récupérer plus rapidement, favorisant ainsi un retour à la productivité plus efficace après chaque pause.
Conformité réglementaire et normes thermiques industrielles
Les normes thermiques industrielles sont nécessaire pour assurer la sécurité et le confort des travailleurs. En France, bien que le Code du travail ne fixe pas de température maximale pour suspendre les activités, l’Institut National de Recherche et de Sécurité (INRS) recommande d’être vigilant lorsque les températures atteignent 28 °C pour les travaux physiques et 30 °C pour les activités sédentaires.
Le respect de ces recommandations nécessite une veille constante et des investissements réguliers dans les équipements de protection. Les employeurs doivent mettre en place des mesures adaptées, telles que l’aménagement des horaires de travail, l’installation de systèmes de ventilation et la fourniture d’eau fraîche, pour garantir des conditions de travail sûres et confortables.
Analyse coût-bénéfice des alternatives anti-chaleur
L’investissement dans des technologies de régulation thermique peut promettre un retour sur investissement (ROI) moyen de 2 à 4 ans. Certaines options de refroidissement industriel permettent de réduire la consommation énergétique de 90 %, ce qui permet de compenser rapidement les coûts d’installation. Une étude de l’Université de Stanford a estimé que l’amélioration thermique permettrait une réduction de 50 % des dépenses énergétiques dans les secteurs industriels.
En définitive, la gestion thermique dans les environnements industriels est importante pour garder la productivité et le confort des employés en protégeant les équipements. L’adoption de choix éco-responsables et innovantes, accompagnée de stratégies organisationnelles adaptées, permet aux entreprises de relever les défis posés par la chaleur en augmentant leur efficacité.