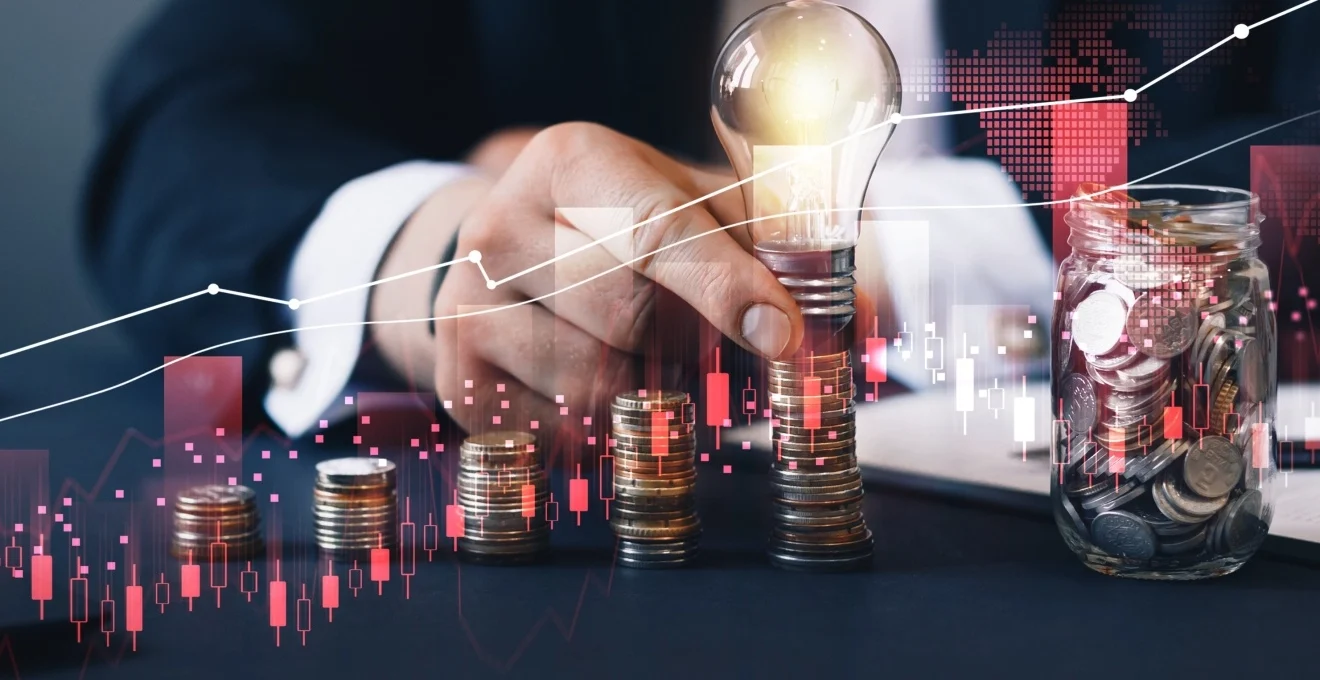
La forte augmentation des tarifs énergétiques observée récemment bouleverse profondément le fonctionnement des sites de production. Alors que l’électricité et le gaz sont une part importante des dépenses, les coûts liés à la fabrication ne cessent d’augmenter, réduisant d’autant la marge nette. Ce contexte contraint les entreprises industrielles à repenser leurs méthodes pour continuer à dégager un bénéfice suffisant. La question se pose donc : comment adapter les processus pour maintenir un équilibre économique ? Quelles pistes peuvent être envisagées pour continuer à rivaliser avec les autres acteurs du marché malgré cette charge supplémentaire ?
Décomposition des charges énergétiques dans l’industrie
Pour évaluer l’effet de la hausse des prix de l’énergie sur la rentabilité d’une usine, il faut d’abord examiner comment cette énergie est utilisée dans les ateliers. Chaque étape de la production repose sur des besoins particuliers en chaleur ou en électricité. En analysant ces usages, on repère les postes les plus sensibles aux hausses tarifaires et les possibilités d’ajustement à court ou moyen terme.
Gaz naturel et procédés à haute température
Le gaz naturel reste incontournable dans de nombreux secteurs industriels, notamment lorsqu’il s’agit d’atteindre des températures élevées. La montée brutale de son prix — parfois multiplié par cinq en Europe — a provoqué une augmentation directe des coûts dans certaines branches. Dans la métallurgie, par exemple, où il alimente les fours, cette hausse peut peser lourdement sur l’ensemble des dépenses de production.
Les industriels doivent désormais composer avec cette instabilité tarifaire dans leurs projections budgétaires. Certains envisagent de modifier leur manière de produire, en électrifiant une partie de leurs installations ou en testant l’usage du biogaz. Ces pistes restent toutefois complexes à mettre en œuvre rapidement, tant pour des raisons techniques que financières.
Électricité : un poids croissant sur la facture globale
L’électricité alimente la majorité des équipements d’une usine : machines, systèmes de ventilation, chaînes de refroidissement, éclairage… Les fortes hausses observées récemment sur les marchés européens ont parfois fait bondir les prix de plus de 200 %. Pour les entreprises dont l’activité dépend fortement de l’électricité, comme celles du secteur chimique ou de l’aluminium, ces augmentations rendent la situation particulièrement tendue.
Dans certains cas, des sites ont été contraints de ralentir ou suspendre temporairement leur activité, ce qui réduit leurs revenus et leur taux de marge, et les empêche de maintenir un niveau de rentabilité acceptable devant la concurrence étrangère.
Production locale d’énergie verte : un pari sur le long terme
De plus en plus d’entreprises choisissent de produire une partie de leur énergie elles-mêmes, en s’équipant en panneaux solaires ou en turbines éoliennes. Même si la mise en place de ces installations demande des moyens importants, cela permet de mieux maîtriser ses charges énergétiques sur la durée.
Certaines initiatives commencent à porter leurs fruits. Une usine automobile en Allemagne, par exemple, a réduit ses dépenses grâce à un parc éolien installé sur son site. Toutefois, se lancer dans cette voie implique une analyse minutieuse et une anticipation des effets à long terme, tant sur le plan technique qu’économique.
Comment les hausses d’énergie influencent-elles les résultats industriels ?
L’augmentation des charges d’énergie ne se traduit pas toujours par une baisse directe du bénéfice opérationnel. Les entreprises disposent de moyens leur permettant d’en limiter les effets. Connaître ces dynamiques permet de mieux anticiper les périodes instables et de bâtir des réponses adaptées pour maintenir l’équilibre financier.
Réactions à court et long terme devant la variation des prix
La consommation d’énergie réagit peu aux hausses de tarifs sur de courtes périodes, car les installations industrielles restent souvent peu modulables sans modifications majeures. En revanche, sur des horizons plus longs, les entreprises tendent à ajuster leurs pratiques en adoptant des équipements plus sobres ou en modifiant l’organisation des lignes de production.
Révision permanente du seuil de viabilité économique
Dans un cadre de prix instables, les industriels doivent recalculer régulièrement les niveaux à partir desquels leur activité reste rentable. Ce suivi permet de détecter les moments où les charges énergétiques deviennent trop importantes pour justifier la préservation de certains volumes de production.
Prenons le cas d’un site de production de papier : une augmentation de moitié de la facture énergétique peut faire passer l’usine d’une situation équilibrée à une perte nette, si les prix de vente ne suivent pas. C’est pourquoi de nombreux industriels s’appuient sur des projections chiffrées pour anticiper ces évolutions et prévoir les ajustements nécessaires.
Sécuriser les achats d’énergie pour réduire l’incertitude
Pour se prémunir contre les envolées imprévues des prix de l’énergie, une part importante des grands groupes industriels choisit de sécuriser une partie de leurs approvisionnements. Cela se fait par des contrats à prix fixes ou par des dispositifs financiers permettant de lisser les variations.
Une enquête récente a montré que les trois quarts des principales entreprises industrielles européennes avaient recours à ces pratiques. En verrouillant certains niveaux de prix, elles parviennent à maintenir une certaine stabilité dans leurs coûts d’exploitation, ce qui leur permet de calculer la marge nette eu plus juste et de la préserver même lorsque les marchés deviennent instables.
Réduire les dépenses énergétiques grâce à l’amélioration des méthodes de production
Avec la de forte hausse des tarifs énergétiques, les usines doivent revoir en profondeur leur manière de produire si elles souhaitent préserver leur équilibre financier. Cela passe par une transformation des pratiques, l’adoption d’équipements performants et une gestion plus affinée des ressources disponibles.
Isolation thermique : un moyen souvent sous-estimé
Renforcer l’enveloppe thermique des bâtiments industriels ou des équipements de production permet de limiter les pertes de chaleur, ce qui se traduit par une baisse des besoins en énergie. Dans certains cas, cela permet de réduire la facture énergétique.
En plus de la réduction des coûts, ce type de démarche améliore aussi l’environnement de travail et peut avoir des effets positifs sur la régularité de la production.
Pilotage automatique de la consommation en usine
Faire appel à des systèmes capables d’ajuster en temps réel la consommation énergétique est un progrès important pour l’industrie. Grâce à des capteurs et à des logiciels d’analyse, les entreprises peuvent mieux adapter leurs machines à la demande, en évitant les excès ou les pertes inutiles. Ces outils permettent aussi une meilleure lecture des charges d’énergie, ce qui facilite la gestion budgétaire et les arbitrages à venir.
Réemployer l’énergie perdue : un potentiel encore trop peu exploité
La chaleur produite par certains procédés industriels peut souvent être captée et réutilisée, au lieu d’être simplement évacuée. Cette énergie dite « fatale » peut couvrir une part notable des besoins d’un site, réduisant les achats externes.
C’est ce qu’a fait une aciérie en Europe, qui alimente désormais près d’un tiers de sa consommation électrique grâce à un système de récupération thermique installé sur ses fours. Cette initiative lui a permis de gagner en autonomie et d’augmenter son résultat d’exploitation de deux points, sans modification majeure de ses procédés de base.
Quand le coût de l’énergie redessine les choix économiques des industriels
L’augmentation rapide des dépenses d’énergie ne relève plus d’un simple enjeu opérationnel. Elle pousse les entreprises manufacturières à repenser en profondeur leurs choix économiques, leur positionnement sur le marché et leurs priorités d’investissement. Ce bouleversement dépasse la gestion quotidienne : il conditionne leur trajectoire future.
Investir dans des équipements moins énergivores implique souvent de réduire les moyens affectés à d’autres domaines : communication, recherche, développement de nouveaux produits, ou politique de distribution des bénéfices.
Certains industriels ont choisi d’engager des transformations de fond en s’équipant de technologies moins exposées aux aléas des marchés énergétiques. Ces investissements, bien qu’importants au départ, peuvent s’avérer bénéfiques à plus long terme, tant pour la maîtrise des charges que pour la stabilité financière.
Cadre légal et mesures de soutien en cas de tensions sur les coûts énergétiques
Pour accompagner les entreprises industrielles confrontées à la montée des dépenses énergétiques, les autorités ont mis en place divers dispositifs visant à limiter les effets financiers et à encourager des pratiques plus respectueuses de l’environnement. Ces dispositifs ont pour objectif de soutenir la compétitivité des industries et de favoriser une évolution vers des modes de production plus durables.
Mesures fiscales et tarifs encadrés pour réduire la facture énergétique
En France, certaines mesures comme la Contribution au Service Public de l’Électricité (CSPE) ou l’Accès Régulé à l’Électricité Nucléaire Historique (ARENH) participent à limiter la volatilité des prix pour les industriels. Ces dispositifs permettent à certaines entreprises d’acquérir une partie de leur électricité à un tarif contrôlé par l’État, ce qui atténue la pression sur leurs budgets énergétiques.
Programmes d’aide pour accompagner la transformation énergétique
Pour soutenir la transition des usines vers des modèles moins consommateurs d’énergie fossile, plusieurs plans d’aide ont été lancés. En France, le plan France Relance a consacré 1,2 milliard d’euros à la décarbonation de l’industrie, avec un focus important sur l’efficacité énergétique. Ce dispositif a déjà soutenu plus de 140 projets, notamment en finançant jusqu’à la moitié des investissements pour les petites et moyennes entreprises.
Systèmes de gestion énergétique : un avantage reconnu
Adopter un système de management conforme à la norme ISO 50001 aide les entreprises à structurer leur démarche d’amélioration énergétique. Cette certification dépasse la simple réduction des coûts : elle renforce également la réputation des industriels et leur accès à certains marchés sensibles aux questions environnementales.
Conséquences financières pour les industries manufacturières
La montée rapide des prix de l’énergie influence fortement le secteur industriel, entraînant des tensions sur les marges des entreprises manufacturières. Cette situation oblige ces dernières à réévaluer leurs méthodes de gestion des coûts et leurs stratégies commerciales. Dans ce contexte, il est nécessaire d’examiner comment les industriels ajustent leurs pratiques pour affronter ces pressions et quelles décisions financières ils privilégient afin d’assurer leur pérennité.
Révision des stratégies de tarification des produits finis
La montée des coûts liés à l’énergie conduit les entreprises à ajuster leur politique tarifaire. Cette révision doit prendre en compte la hausse des charges de production, mais aussi la sensibilité des clients aux variations de prix ainsi que la position de l’entreprise vis-à-vis de ses concurrents.
Réallocation des budgets et arbitrages financiers
Sous la pression exercée sur les marges, les entreprises doivent redéployer leurs ressources de façon réfléchie. Cela suppose souvent des décisions délicates entre différents postes de dépenses tels que la recherche et développement, la communication, les investissements matériels ou encore la distribution de dividendes.
Investissements dans les technologies durables
Bien que ces investissements demandent des ressources importantes au départ, ils apportent des perspectives intéressantes en matière de retour sur capital engagé et de positionnement pérenne. Ils permettent de réduire la dépendance aux énergies fossiles, mais aussi de se préparer aux évolutions réglementaires à venir.
Par ailleurs, ces initiatives ouvrent la porte à de nouveaux marchés. Ainsi, une entreprise chimique ayant investi dans des procédés utilisant de l’hydrogène produit à partir d’énergies renouvelables a pu lancer une gamme de produits « écologiques », conquérant ainsi une part importante de clients attachés à réduire leur empreinte environnementale.